Ceramic Welding Pins made of Silicon Nitride for maximum Service Life in Projection Welding
Ceramic materials have long replaced metal in the production of welding pins, which ensure a perfect fit for sheet metal and nuts in projection welding and are subject to temperatures of up to 800°C. Gas-pressure sintered silicon nitride ceramics from CeramTec are at a distinct advantage here.
Metal simply can’t compete with advanced ceramics with regard to insulating properties, resistance to temperature change, and minimal wear and tear due to the high degree of hardness and durability. Yet another advantage of using ceramics for centering pins is their smooth polished surface, which prevents welding spatter from adhering. However, service life does face limitations when it comes to welding pins made of commonly used zirconium oxide ceramics. Over time, this material is likewise unable to stand up to the 30 to 40 kiloamperes that flow through the copper electrodes in projection welding and the required working temperature of 800°C, and thus suffers from wear. The solution: Centering standard molds made from silicon nitride ceramics.
Centering Pins made of Silicon Nitride Ceramics easily outperform Zirconium Oxide and Metal
CeramTec developed the SL200B silicon nitride ceramic material especially for use in projection welding. This silicon nitride ceramic is a 100 bar gas-pressure sintered, high-strength, black material with impressive properties. And it boasts decisive advantages compared to zirconium oxide or even metal when used for welding pins:
CeramTec SL200B silicon nitride ceramics stand up to tough projection welding conditions most effectively and deliver a significantly higher service life. Comparison: While commonly used ceramic welding pins provide service lives 40 times that of metal, the service life of CeramTec silicon nitride ceramics is an additional five times greater than that of centering pins made from zirconium oxide.
Highly Economical Projection Welding
Silicon nitride ceramic centering pins only need to be replaced about once a month.
Ceramic welding pins made of silicon nitride significantly increase service life and enable high levels of precision and greater accuracy over extended periods in projection welding. Metal welding pins often need to be replaced several times a day due to wear and adhering slag, whereas centering pins made of silicon nitride ceramics only need to be replaced about once a month.
And generally these pins only require replacement when damaged by mechanical force. This not only provides more economical production thanks to a reduction in costs, but also makes the entire process more robust, which in turn results in consistently high product quality.
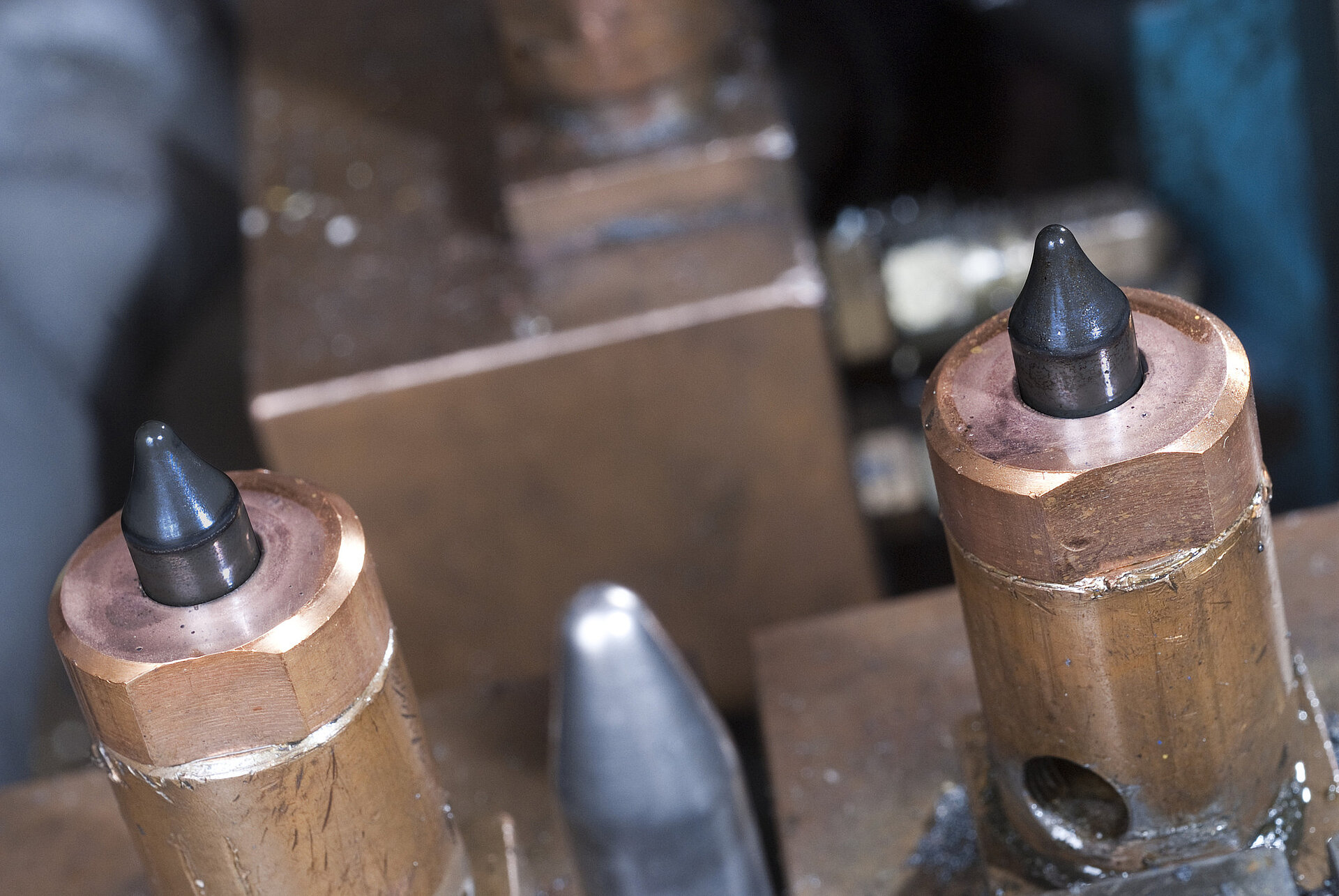
Retrofitting to black Centering Pins made of Silicon Nitride
Old centering pins on the machine can be retrofitted to silicon nitride seamlessly and do not require conversion.
Retrofitting welding pins from steel to ceramic is simple. Ceramic centering pins from CeramTec can be attached to the machine using threads, adapters or a plug-in mechanism. What’s more, switching from standard ceramics to SL200B silicon nitride ceramics from CeramTec does not result in additional costs: From a price standpoint, this material developed by CeramTec is almost identical to commonly used zirconium oxide.
CeramTec provides customers made-to-measure designs and geometries according to specification – even for small quantities. What’s more, SL200B silicon nitride ceramic is black: The dark color contrasts well with the workpiece, enhancing work precision as the pins can be more easily distinguished from the metal. Our ceramics experts will gladly answer any questions you may have about materials, centering pin and centering standard mold geometry options, the range of products available from CeramTec or how to retrofit your projection welding machine.
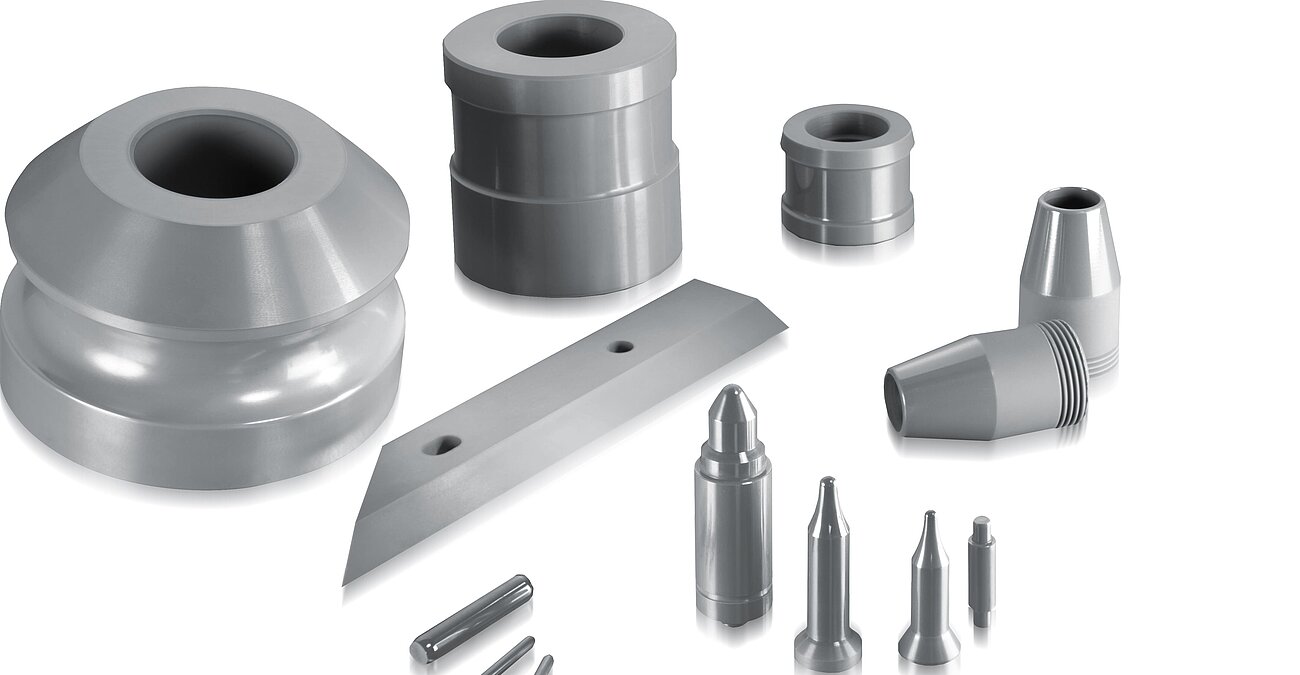