Customised Ceramic Solutions for Wear Protection
ALOTEC® high-performance ceramics fulfil the highest requirements as a material, even under difficult conditions such as wear, corrosion and high temperatures. Based on material expertise, a comprehensive understanding of wear protection applications and many years of project and process experience, CeramTec-ETEC (part of the CeramTec Group since 2008) has established itself as one of the world's leading suppliers of ceramic wear protection solutions.
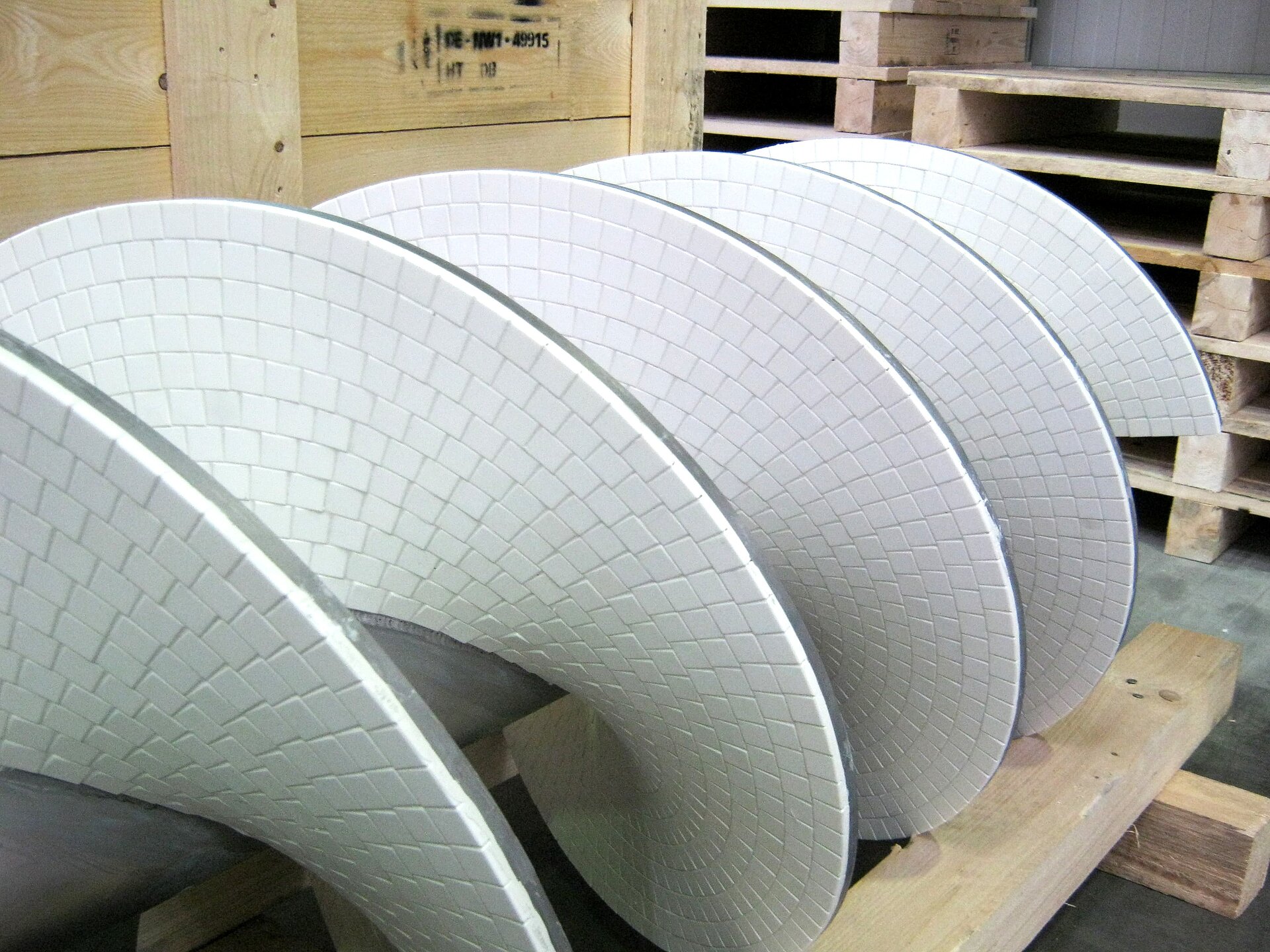
From the raw materials and steel industries to the chemical and food industries, ALOTEC® solutions are used in a wide variety of sectors and applications - in all steps along the material preparation process chain: from conveying and transporting raw materials to grinding and separating, mixing and stirring. ALOTEC® is convincing both in comparison with other materials and with other ceramic materials.
Why ceramics are generally an excellent choice for your wear protection application and what advantages do you have with CeramTec as your partner? You can find out this and more in our wear protection brochures!
Transport and Conveying
We develop and realise reliable wear protection solutions for various transport systems and wear-prone components in the processing industry - from the extraction of raw materials to the use of the end product.
Depending on whether solid, liquid or gaseous products are being transported, different transport systems such as pipe systems, bends, channels, troughs, hoppers or containers are used. The material is transported pneumatically, mechanically (screw conveyors, conveyor belts) or by gravity.

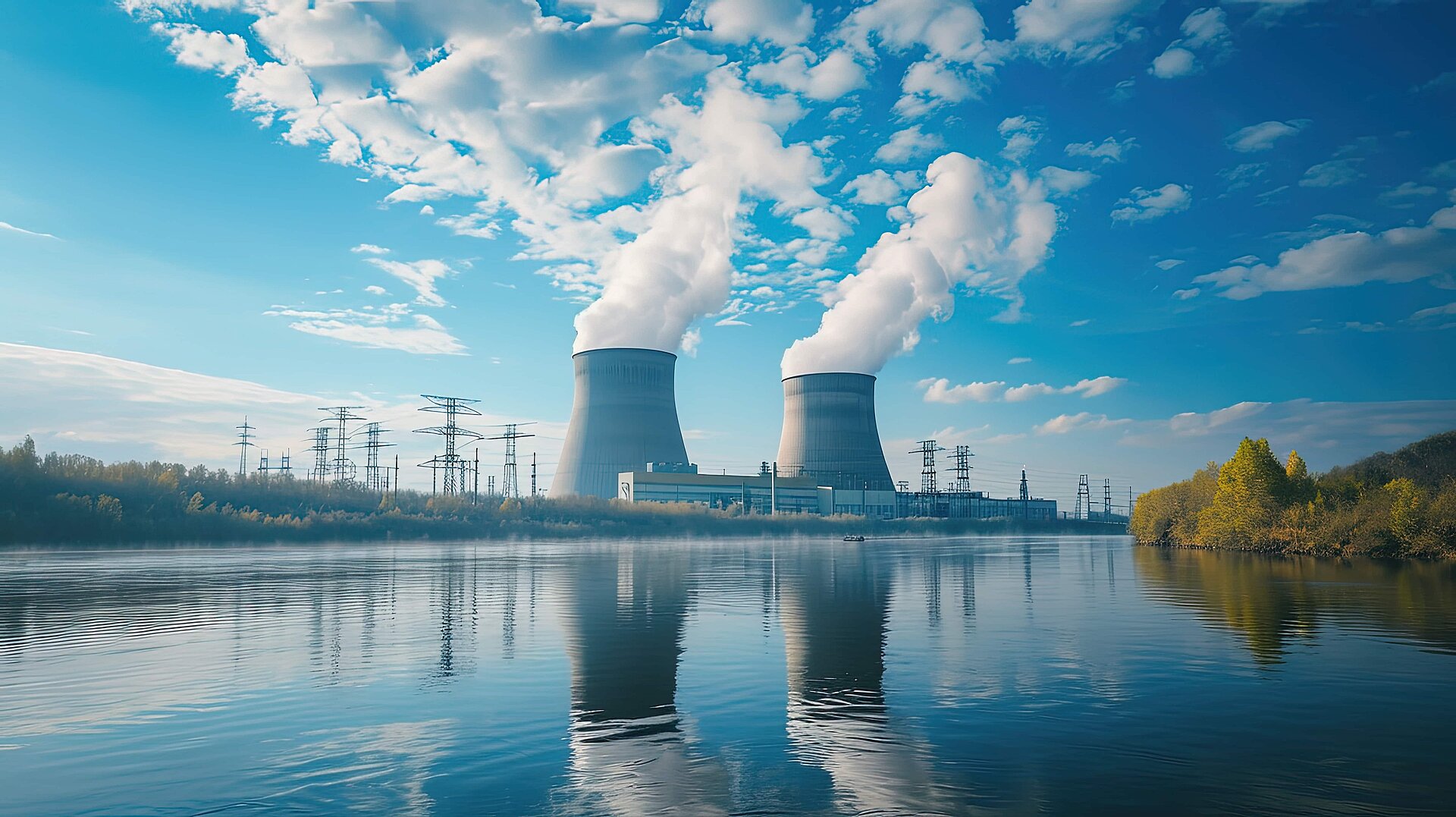
Crushing and Grinding
Industrial grinding requires purity - especially when grinding foodstuffs or animal feed, pharmaceutical products, pigments or colours, but also raw materials for the glass and ceramics industries, for example.
ALOTEC® mill linings for drum mills minimise impurities through low abrasion and thus prevent contamination of the material to be ground. They outperform conventional linings in terms of wear resistance during wet and dry grinding and also score points with their high throughput rate and long service life. The smooth surfaces of the mill liners ensure even lifting and rolling of the grinding balls and have therefore proven their worth in fine grinding. Depending on the desired grinding result, lifter and shaft profiles can also be realised.
Classifying and Separating
Various processes such as sieving, but also the use of cyclones or classifiers, are used when it comes to classifying materials in industrial production.
Classifiers are used in fine grinding plants to separate the finely ground material for further production steps. In classifiers, the parts that come into contact with the product, such as the housing, discs and wheels, can be protected with ALOTEC®. Classifier separators (aerocyclones) are mainly used in power stations, waste incineration plants and steelworks and are used to separate fine solids from the air flow as completely as possible. In the polyurethane/ALOTEC® composite, hydrocyclones offer particularly high resistance to wear and corrosion and are lighter than other solutions and impact-resistant thanks to the PU coating. The most important applications are currently the recycling of waste paper and the separation of raw kaolin.
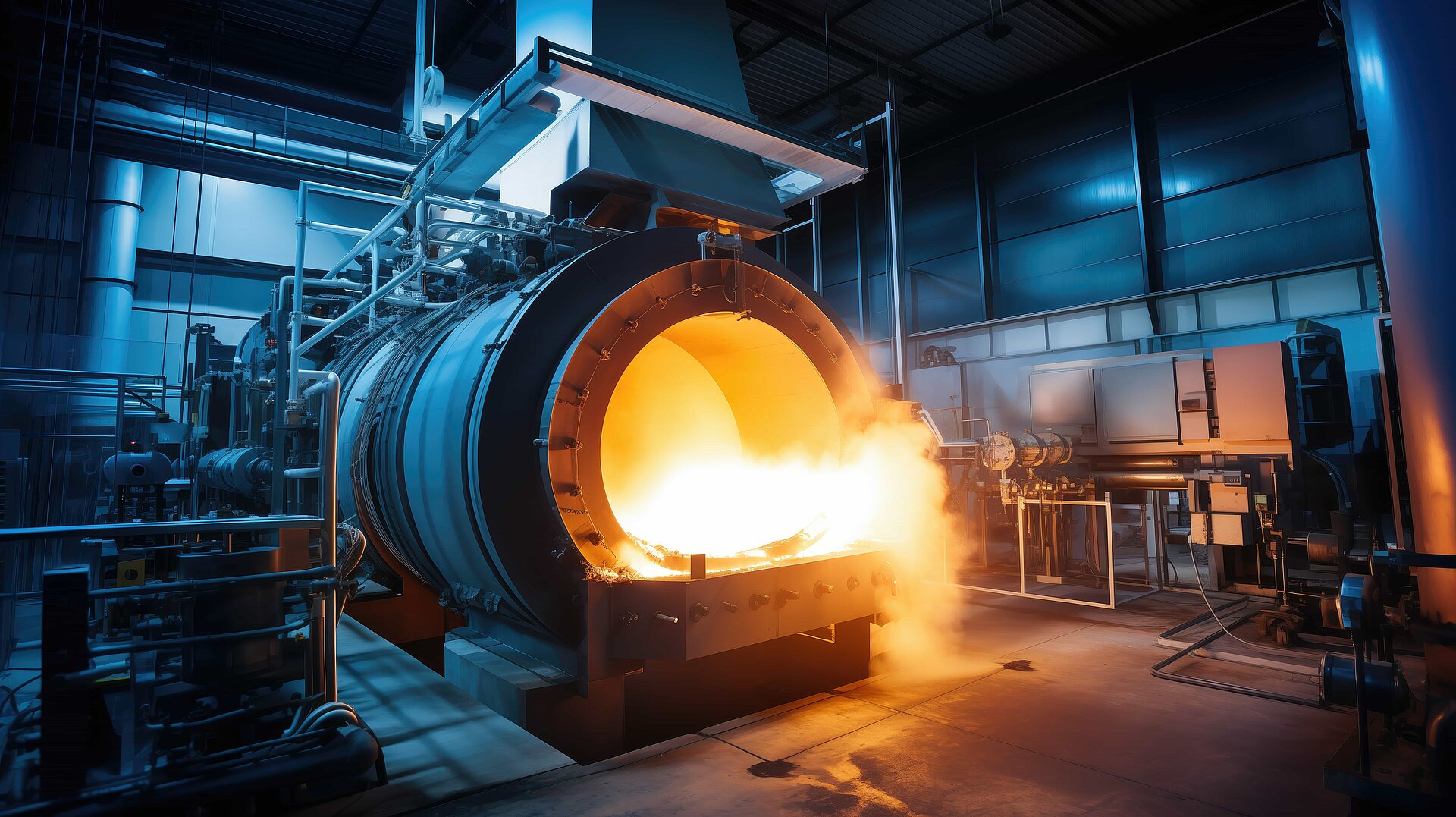
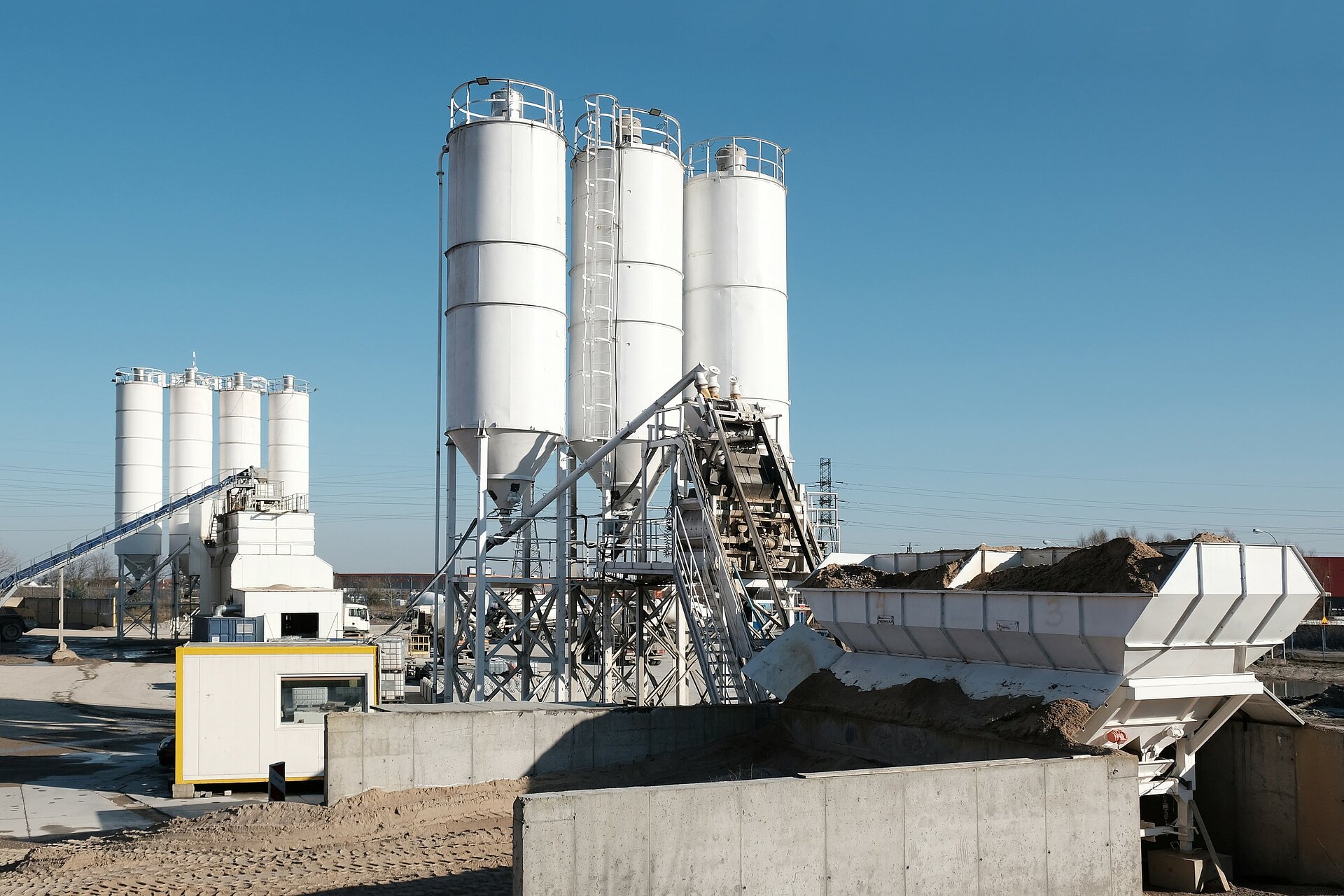
Mixing and Stirring
Mixing is one of the most wear-intensive processes in processing technology.Based on our experience with various industrial mixing plants, we successfully plan and realise wear protection solutions that meet your specific requirements - from the on-site assessment and material recommendation to the 3D design and complete realisation of the ceramic lining.
A special laying technique avoids continuous joints in the direction of stress. Together with close-jointed installation and specially cut parts for curved shapes, wear is significantly reduced and service life is extended. At the same time, energy savings and shorter cleaning times can be achieved. The low-friction mixing paths achieve better homogeneity of the mix and prevent caking.
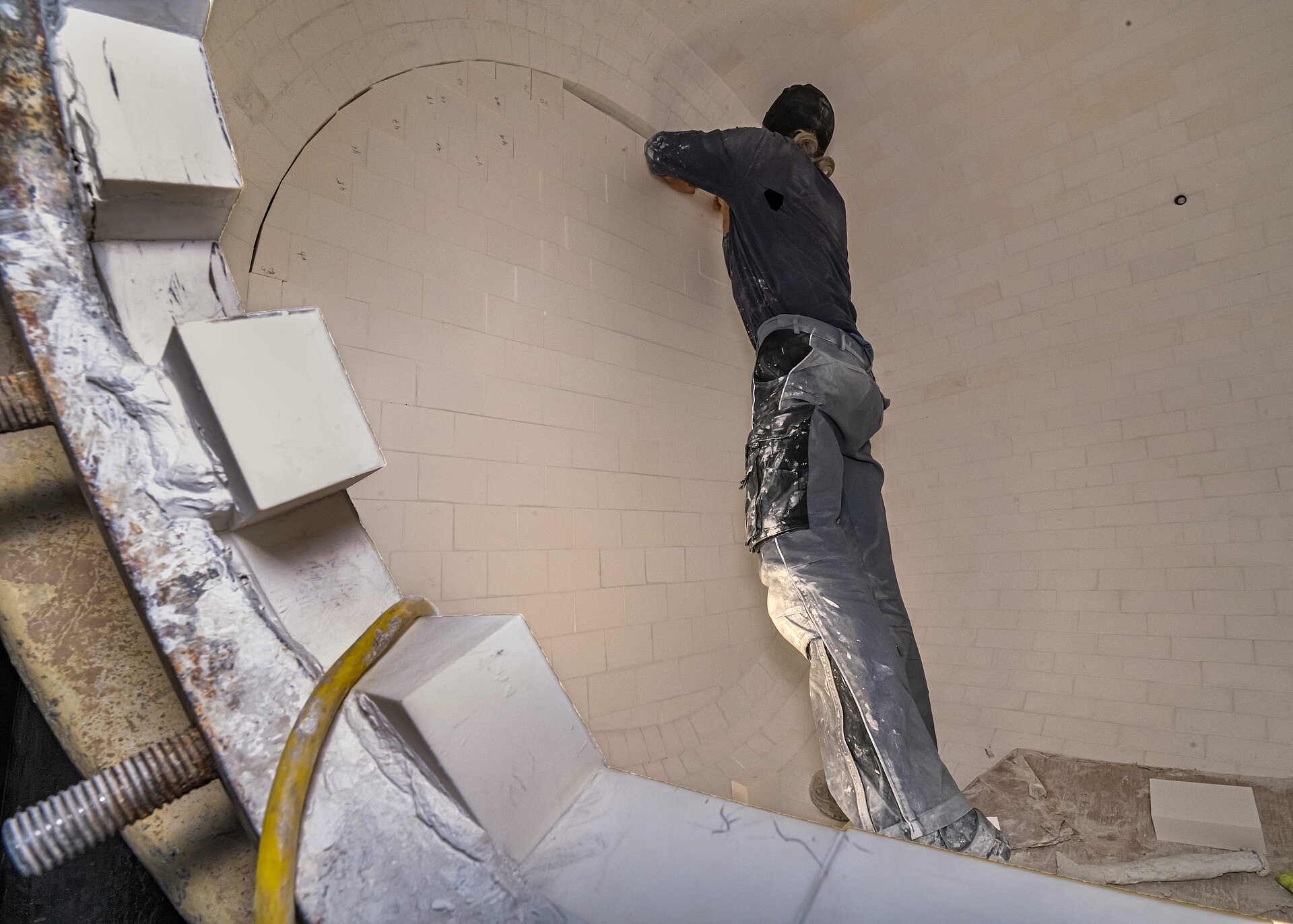
Service
Effective wear protection begins with a design that is appropriate for the application and material.The basis for this is a system analysis that takes comprehensive account of the mechanical, thermal and corrosive loads on a system.
Whether wear protection linings for tanks or piping systems or complex ceramic components for machines and systems such as measuring and control elements, ball valves, hydrocyclones, bearings, nozzles, pitot tubes, lances or even ceramic composite systems with steel, polyurethane or rubber - we see ourselves as problem solvers for your specific wear protection application.
We support you from the system inspection and individual consultation, through the recommendation of the right material and its processing and installation, the on-site measurement survey to the CAD-supported creation of the optimum installation plan and the final implementation.
We look forward to discussing the individual requirements of your wear protection application with you.