Ceramic Tools for the Welding Process
There is only one material that minimizes welding process wear and ultimately extends tool service life: silicon nitride advanced ceramic.
CeramTec has developed a special silicon nitride ceramic for use in the welding process that is the most suitable material for welding tools such as welding rollers, centering pins and gas nozzles. The outcome: Welding process components featuring remarkable hardness and wear resistance, and very high temperature and chemical resistance. They vastly extend service life, reduce overall retooling times, extend machine running times and enhance end-product quality. In other words: Silicon nitride ceramics create added value in the welding process.
Silicon Nitride Ceramics – The Ideal Material for Use in Welding Processes
CeramTec developed a silicon nitride material specifically for the high demands in this joining method which ensures long service life and improved precision with minimal wear. In addition to high flexural strength and hardness, this 100 bar gas-pressure sintered ceramic material particularly excels with high compressive strength and thermal shock resistance. Yet another advantage is the electrical insulation provided by this silicon nitride ceramic.
“Compared to other ceramic materials, silicon nitride is clearly the better choice overall for the extreme demands in the welding process.”
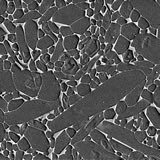
The SEM image shows the non-porously arranged, hexagonal, needle-shaped silicon nitride crystals. These crystals are interlocked, resulting in extraordinary material toughness. The homogeneously dispersed glass fibers shown as white areas in the image create the excellent high-temperature properties.
Gas-pressure Sintered Silicon Nitride Ceramic
Although advanced ceramics like yttria-stabilized zirconium oxide have been used for welding pins and aluminum oxide for gas nozzles for many years now, silicon nitride offers numerous advantages as an alternative material for welding processes. The few disadvantages, such as its somewhat lower flexural strength, can easily be compensated for with proper component construction and design suitable for ceramics.
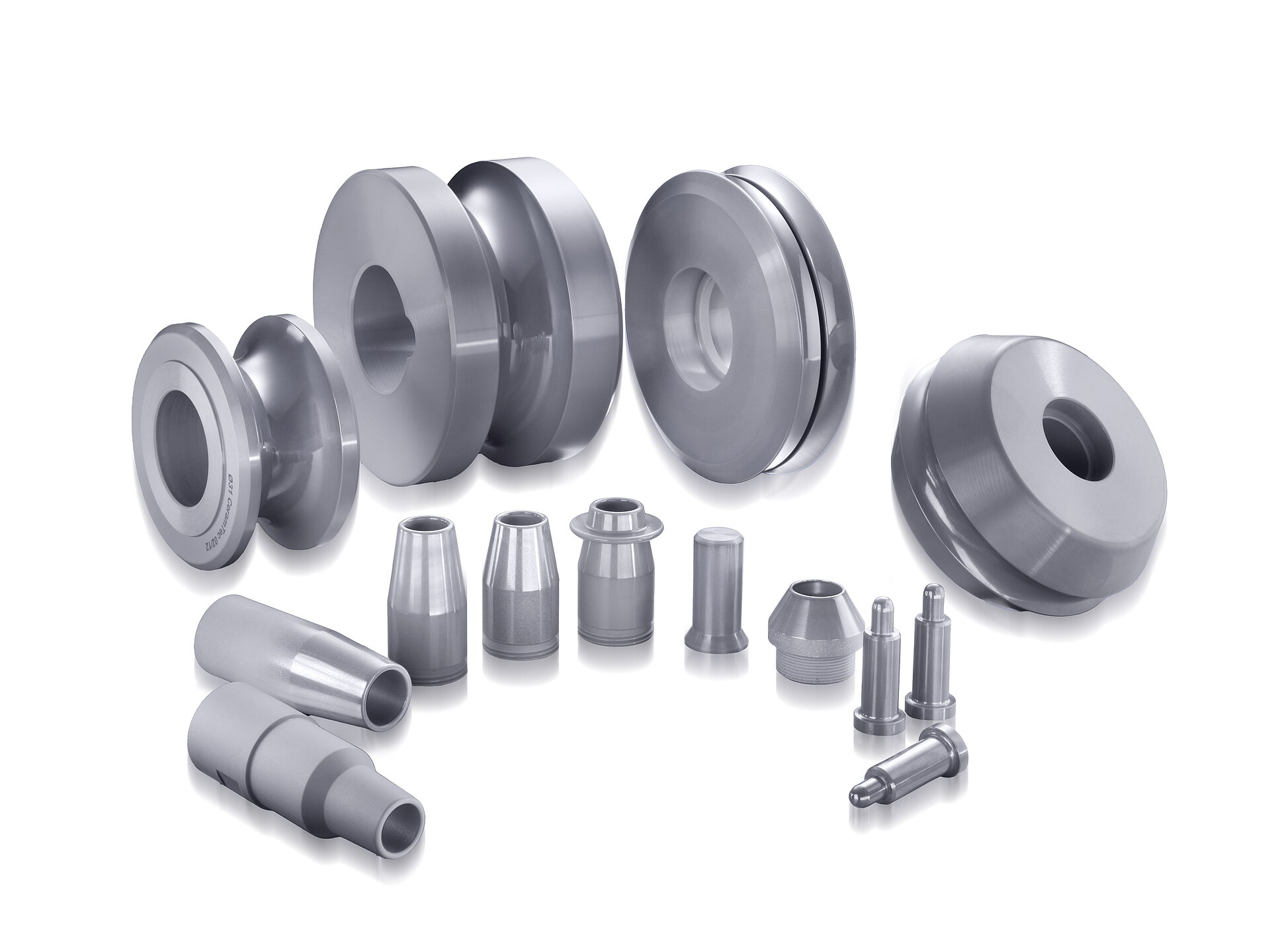
Material property | Unit | Silicon nitride SL200B | Zirconium oxide | Alumina |
Gas-pressure sintered | yttria-stabilized | 99,70% | ||
Density | g/cm³ | 3.21 | 6.04 | 3.95 |
Mechanical properties | ||||
Compressive strength | MPa | 3,000 | 2,200 | 2,500 |
Flexural strength | MPa | 850 | >1,000 | 300-400 |
Vickers hardness | HV | 1,650 | 1,240 | 1,600 |
Average roughness Ra | μm | 0.05 | 0.10 | 0.10 |
Thermal properties | ||||
Thermal conductivity | W/mK | 21 | 3 | 28 |
Max. operating temperature | °C | 1,300-1,600 | max. 1,000 | 1,300-1,500 |
Thermal shock resistance | °C | ca. 700 | ca. 300 | ca. 150 |
CeramTec’s material SL200B/BG is used in every area of the welding process – for welding rollers, as centering pins, when sheet metal and nuts require exact positioning in projection welding, or as gas nozzles, in order to achieve an even flow of shielding gas in MIG/MAG welding. All products can be easily retrofitted in existing machines.
CeramTec is always the right partner to contact, even for new application areas. Our ceramics experts will gladly provide you with advice on how to increase process reliability and answer your questions on using technical ceramics in the welding process.