Metal Matrix Composite (MMC)
The range of applications for high-strength light metal components – primarily aluminum, but also magnesium and titanium – is constantly growing. The motivation for using light metals in the automotive industry is to reduce weight and ultimately lower fuel consumption and emissions.
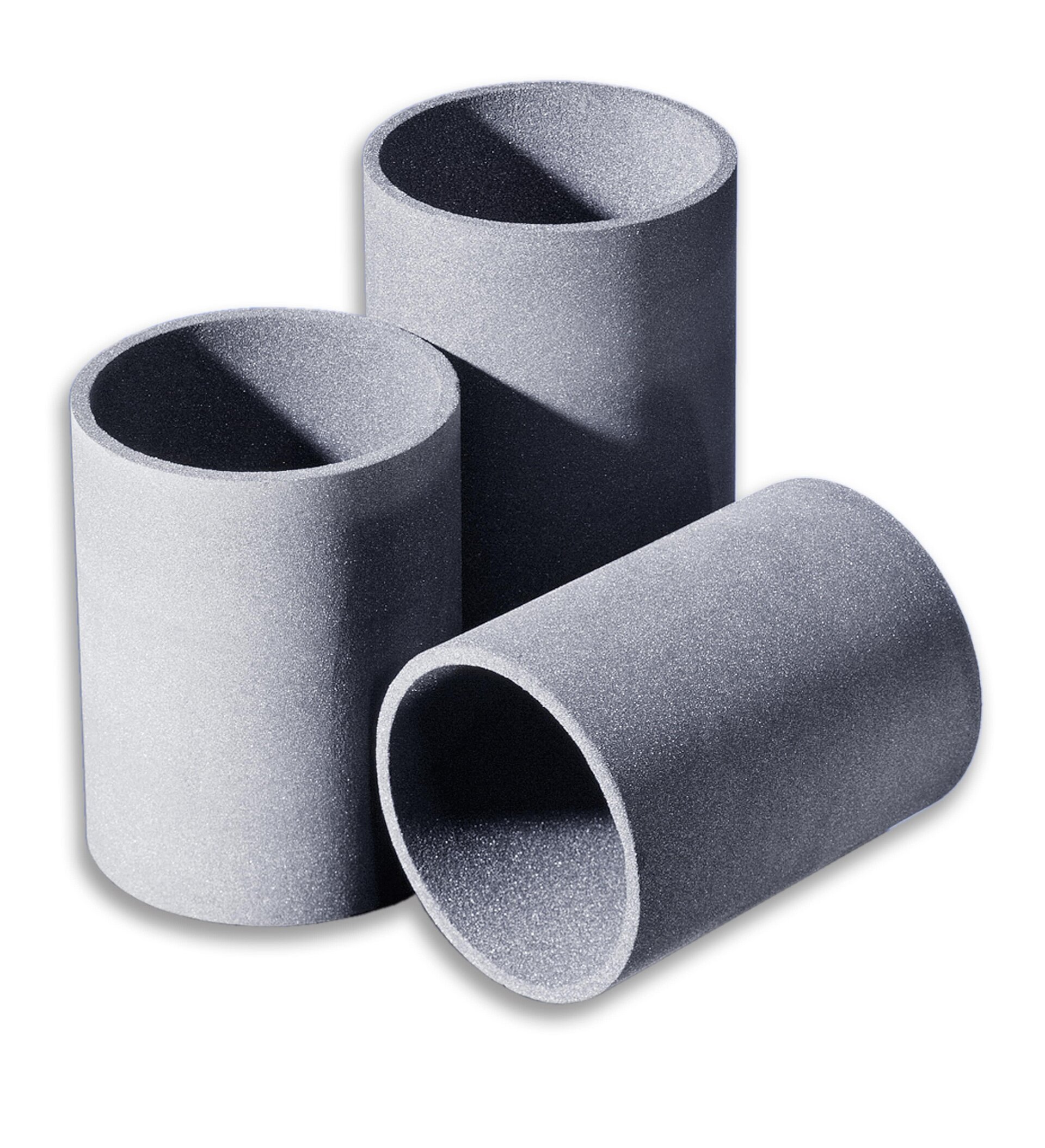
However, light metal construction reaches its limits where it has to withstand high tribological, mechanical or thermal loads. The solution is the targeted reinforcement of lightweight components at the points of maximum stress. Such composites of metal and ceramics, so-called metal-matrix composites (also: metal-matrix composites, MMC), consist of a metal (matrix) reinforced with hard ceramic particles.
The result is a product that has the advantages of both materials, namely the low weight of metal on the one hand and the high performance of ceramics on the other.
Application examples for metal-ceramic composites:
- Antenna waveguides in the Hubble Space Telescope
- Commercial satellites
- Automotive industry, e.g. cylinder liners and brake discs
- Aerospace, e.g. rotor blade sleeves in helicopters
Recent innovations have significantly reduced the production and machining costs associated with MMCs. As the world's leading supplier of technical ceramics, CeramTec has developed a process to produce lightweight MMC components efficiently and economically while maintaining the highest quality standards.
CeramTec's highly porous ceramic preforms are infiltrated by the molten metal during the casting of the MMC product. This creates a continuous transition between metal- and ceramic-reinforced areas. Our preform technology opens up a wide range of new applications.
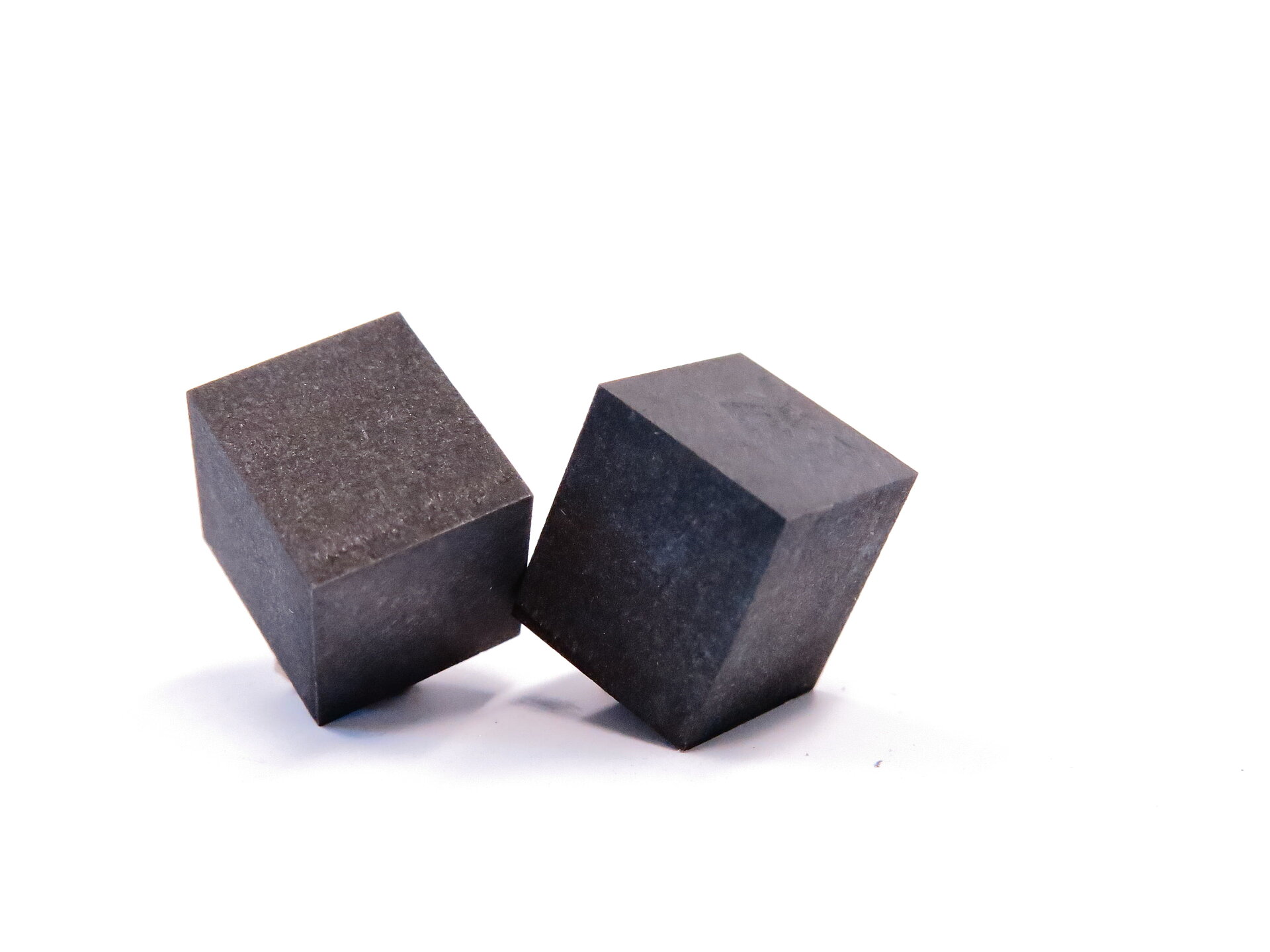
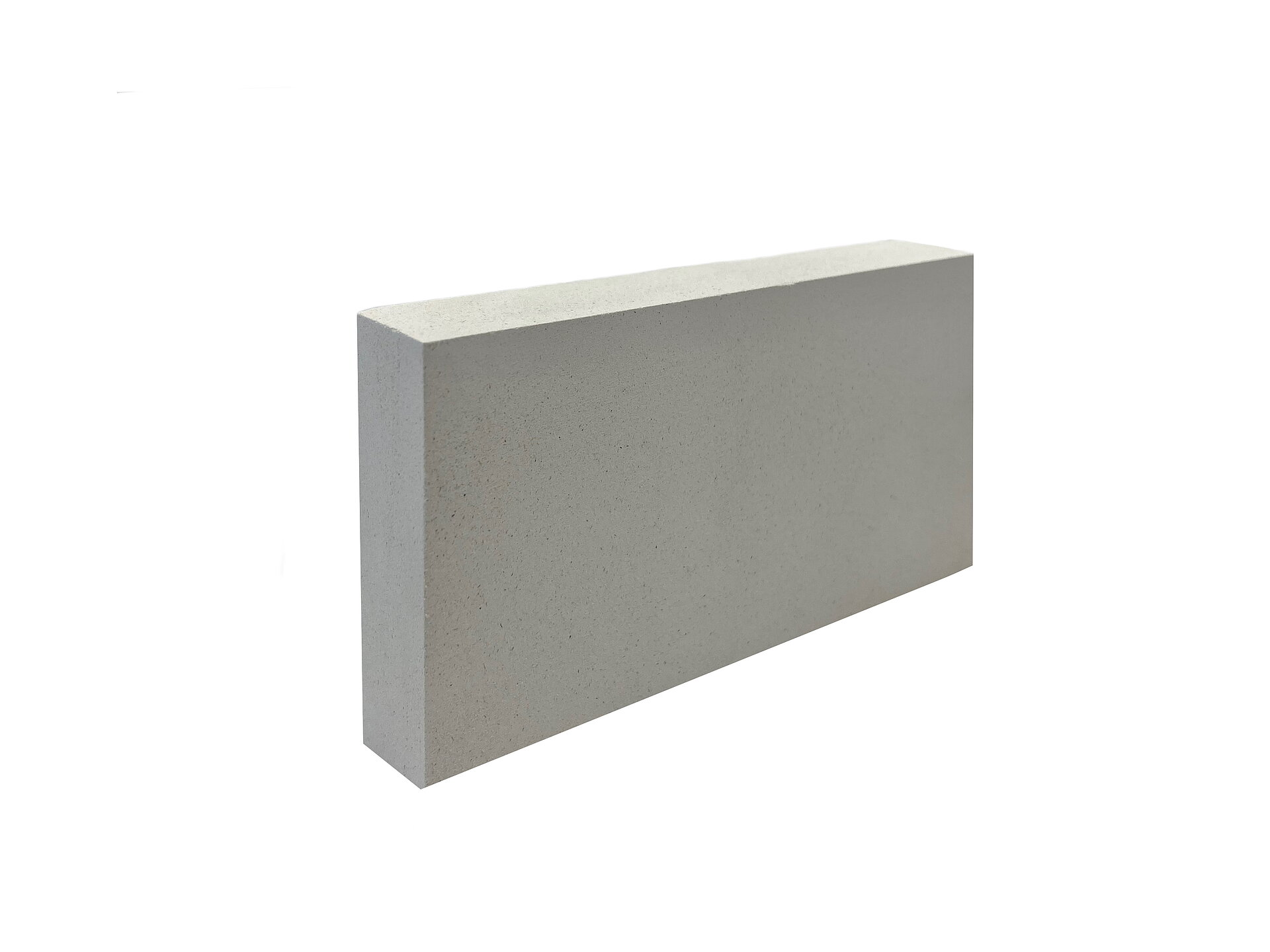
Preform Technology
CeramTec's MMC preforms are tailored to the needs of our customers and can be used with standard aluminium alloys.
CeramTec offers a ceramic content between 35 and 70%, whereby grain and pore sizes are equally adjustable. For high performance products, an additional hardening additive can be used to further improve the properties. Diverse and complex geometries are possible with this manufacturing process.
Our preform concept, combined with our tooling expertise, offers improved performance as well as lower total cost of ownership. Our preform portfolio includes a wide range of standard oxide and non-oxide ceramic materials.
Silicon carbide (SiC) preforms
A SiC preform is perfect for tribological optimisation. The use of a SiC preform offers higher thermal conductivity and improved abrasion resistance. An example of MMC components made of silicon carbide are brake discs. Due to the improved abrasion resistance, MMC brake discs produce fewer brake dust emissions, have a significantly longer service life and a weight reduction of about 50 % compared to conventional grey cast iron discs.
Aluminum oxide (Al2O3) preforms
For applications with highly stressed mechanical components, an MMC made from an aluminium oxide preform is an excellent choice. This material exhibits high flexural strength, increased modulus of elasticity and good fracture toughness.
An example of an application of MMC made from alumina preforms is a bearing bridge in an engine. The local reinforcement of the surrounding light metal area by the MMC allows for more complex designs and lower weight due to the 100% increase in modulus of elasticity and 75% increase in strength.
Since the thermal expansion of the MMC and the surrounding material are close to each other, less thermal stress is generated compared to a standard cast iron bearing bridge.
Machining
Increasing the amount of ceramic particles in the MMC preform can be a challenge for our customers' subsequent hard machining processes. CeramTec's expertise in hard machining of ceramic materials and manufacturing of ceramic cutting tools ensures that we have the knowledge to support our customers through the entire manufacturing process.
CeramTec also develops cutting tools for MMCs and offers options with undefined cutting edges. We offer laser cutting for high precision requirements and waterjet cutting for faster metal removal rates.
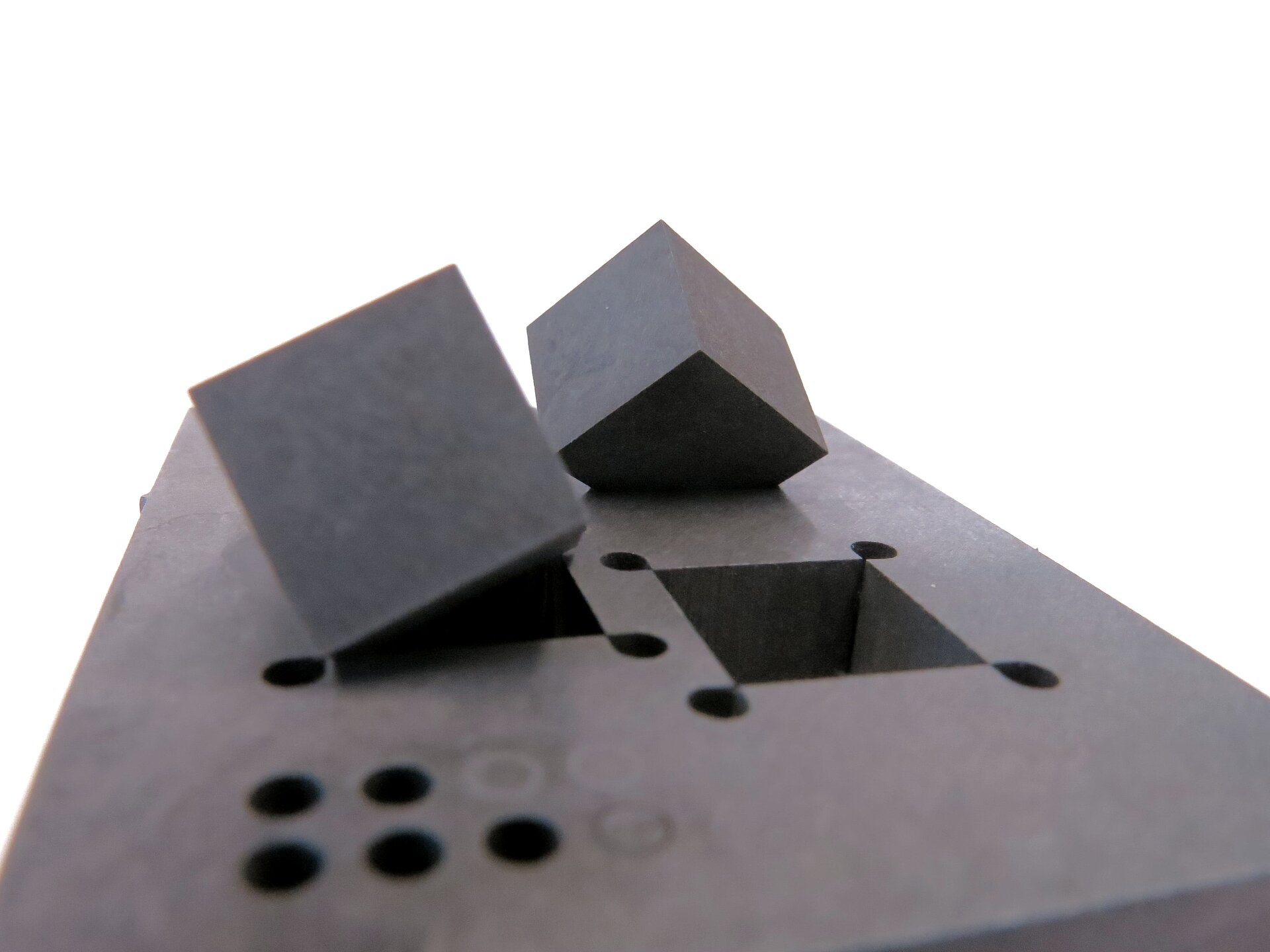