Cleaning Transducers
CeramTec produces ultrasonic cleaning transducers that deliver high performance in the harshest industrial environments. They can be used in continuous mode, or intermittently, and have a proven track record in ultrasonic cleaning applications as diverse as cleaning semiconductors and engine parts.
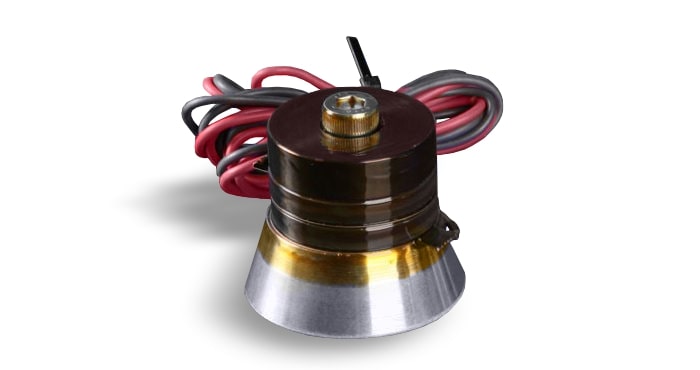
Our ultrasonic cleaning transducers can be supplied with exposed contacts for soldering or complete with flying leads. All our standard products are varnish treated to minimize resistance to humidity and other atmospheric conditions, and come complete with a grit-blasted base for good adhesive bonding in tanks. A thread for stud mounting is optional.
Standard products and bespoke solutions are available for medical, industrial, automotive, electronic and other cleaning applications.
Bonding Ultrasonic Cleaning Transducers to Tanks
We recommend a heat-cured adhesive to give consistent bond strength and optimum transducer efficiency.
1. Preferred Glue
REDUX 312-5 by HEXCEL COMPOSITES (formerly CIBA GEIGY)
This is a single component epoxy material available in sheets. It must be refrigerated to maintain its properties in accordance with the manufacturer’s instructions.
2. Preparation of Surfaces
The tank should be freshly abraded before the bonding takes place. MTC ElectroCeramics' transducers in most case supplied with a grit-blasted based to facilitate bonding and abrasion is therefore not required. Both surfaces (tank and transducers) should be cleaned and degreased with a suitable method prior to bonding.
3. Bonding
After cutting the Redux sheets to size, the protective layers should be removed from it, and the bonding done immediately. Pressure must be applied to the bond either by a weight of at least 6kg or, better, via a jig which applies controlled pressure whilst holding the transducer in place.
The inner surface of the tank should be supported to prevent distortion.
The glue must then be heated in an oven at 125ºC for 30 minutes. The weight should be left in place during the cooling down. To ensure all components reach the curing temperature it is recommended that curing fixtures and/or weights are pre-heated.
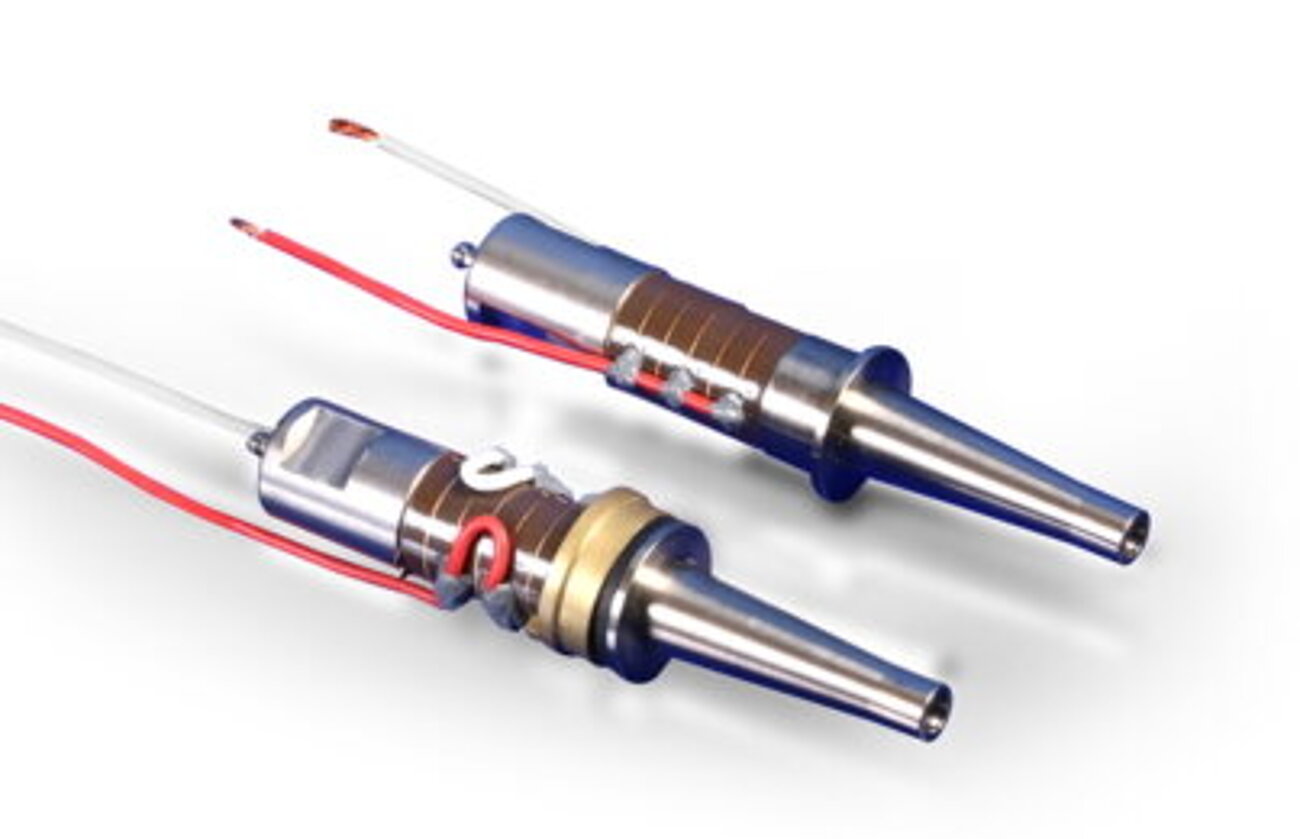