Ceramaseal® Terminals
Ceramaseal® high-alumina ceramic terminals are used to pass electrical power or signal through the case or housing of an electrical apparatus for connection to outside cables or leads.
Applications include transformers, capacitors, filters, power supplies, and cable terminations. Ceramaseal® terminals insulate the conductors from the case and provide a hermetic seal between the inside of the apparatus, which is usually oil or gas-filled, and the outside atmosphere. The insulation within the terminal is a high-alumina ceramic body, usually with a tubular or disc shape. The body provides the terminal with its superior insulating properties.
Bonded to the top or inside diamber of the ceramic body is a metal cap-and-stud or cap-and-lug assembly, which forms the connection point to the outside cable or lead. A metal flange is similarly bonded to the ceramic near the bottom (or the outside diameter of disc-shaped bodies) for mounting to the apparatus case.
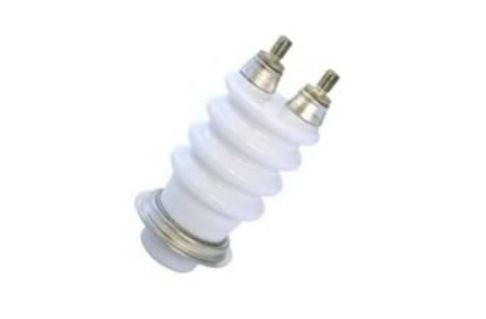
On some terminal designs, the cap-stud or cap-lug assembly is integrated with a conductor passing through the hollow inside of the body. This conductor is used for the internal connection in the apparatus. On other designs, this internal conductor is inserted by the customer and joined with the cap upon installation of the terminal. Terminal mounting flanges of Ceramaseal® terminals are joined to the apparatus housing by various welding, brazing, and soft soldering techniques.
Ceramaseal® bonding process for high vacuum tightness, strength and high temperature resistance
CeramTec creates the high vacuum tightness, strength, and high temperature resistance of the Ceramaseal® ceramic-to-metal bond with its own proprietary sealing process, a variation of the active alloy technique. The bond between metal and ceramic is chemical, rather than mechanical. Ceramaseal® terminals and assemblies remain hermetic even in extreme environments. Some designs can survive high-temperature bakeouts as well as continuous operation at 350ºC in air. In addition, resistance to thermal shock is excellent; some Ceramaseal® terminals have remained leak tight after repeated direct transfer from liquid nitrogen (-196ºC) to molten solder (+240ºC).
Ceramaseal® high-alumina ceramic (Al2O3) terminals
The insulating bodies on most Ceramaseal® terminals and assemblies are made of high-strength, high-alumina ceramic (Al2O3). Alumina content ranges from 94 to 99.5 percent, depending on the unit and its application. Several properties of high-alumina ceramic make it excellent for use in Ceramaseal® insulating terminals:
- High dielectric strength, even at high temperatures
- High thermal conductivity and high mechanical strength enable Al2O3 to survive severe thermal shock
- Alumina is an extremely dense material, is gas tight in thicknesses greater than 0.0127 cm (0.005") and absorbs no water. Because of these properties, Al2O3 provides reliable insulation even in the presence of contamination and extreme humidity.
Ceramaseal® alumina ceramic blanks for terminal bodies are made using a number of methods, including extrusion, isostatic pressing, and die pressing. After forming, the ceramic blanks are fired in high-temperature kilns, then coated with a high-temperature glaze which matches the ceramic in expansion coefficient. In service, the glazed surface stays cleaner than unglazed ceramic, thus permitting maximum voltage before corona or flashover occurs. And when cleaning does become necessary, the operation is easier with glazed ceramic.
Cap and flange materials on Ceramaseal® terminals
Caps and flanges on Ceramaseal® terminals and assemblies are made of Kovar® or a nickel-iron alloy containing coefficients close to that of alumina ceramic. CeramTec can also produce assemblies with copper caps and flanges as well as successfully bond high-alumina ceramic to such metals as nickel, platinum, and cold-rolled and stainless steel. Caps and flanges are supplied with or without hot solder dip finish, as specified by the customer. Solder dipping is performed in accordance with Specification MIL-F-14072, finish number M-258 Type II.
Composition and Linear Expansion Coefficients of Kovar® and Ceramaseal® Nickel-Iron Alloy
Material | Composition % | Coefficient of linear expansion IN./IN.°C | ||
---|---|---|---|---|
42% nickel-iron | 93°C to 2,4°C | 316°C to 427°C | ||
Iron | 57,15 | 5,35 x 10-6 | 9,90 x 10-6 | |
Nickel | 42,00 | |||
Manganese | 0,50 | |||
Silicon | 0,25 | |||
Carbon | 0,10 (max) | |||
Kovar® | 30°C to 200°C | 30°C to 450°C | ||
Iron | 53,7 | 4,33 x 10-6 to 5,30 x 10-6 | 5,03 x 10-6 to 5,37 x 10-6 | |
Nickel | 29,0 | |||
Cobalt | 17,0 | |||
Manganese | 0,3 |
Vacuum-tube-grade bonding alloys
Only vacuum-tube-grade alloys are used in Ceramaseal® products. A typical Ceramaseal® terminal is bonded with a silver-copper eutectic with a melting point of 780°C. CeramTec also uses other metals and alloys successfully, including pure silver (melting point: 961°C) and a gold-nickel alloy (melting point: 950°C).
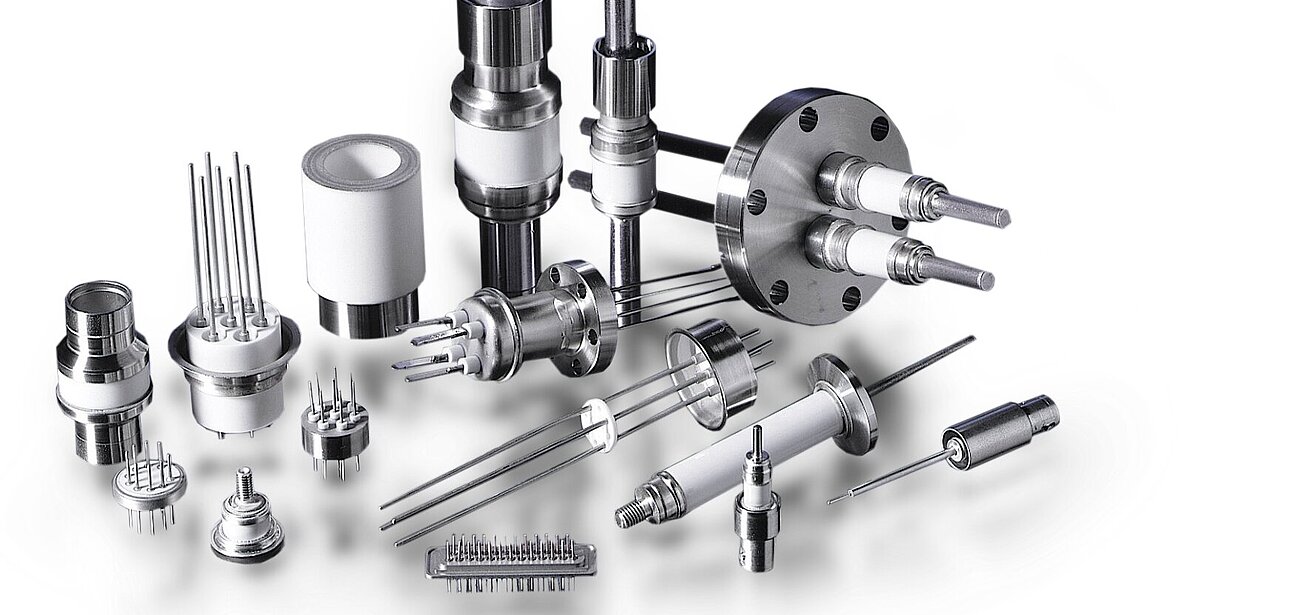