Keramische Membranen für Drucksensoren
Ob in Medizintechnik, Lebensmittelproduktion, Klima- oder Chemietechnik – konsequente und zuverlässige Drucküberwachung mittels moderner Drucksensorik ist entscheidend für eine Vielzahl industrieller Anwendungen. Je nach Sensortechnologie kommen verschiedene keramische Elemente aus Aluminiumoxid zum Einsatz und tragen zum perfekten Zusammenspiel zwischen Sensor- und Transformationselement und damit zur Genauigkeit der Messergebnisse bei.
Dabei sind die Anforderungen an die keramischen Komponenten so vielfältig wie die verschiedenen Messanwendungen selbst. Bei kapazitiven Messtechnologien bilden ein keramischer Träger und eine durch Druck verformbare keramische Membran die beiden Kondensatorplatten. Unter Druck wird der Abstand zwischen den beiden Platten kleiner, die Kapazität verändert sich, da die Belastung die Membran verformt.
Resistive Drucksensoren auf Keramikbasis verwenden metallische Dehnungsmessstreifen, die im Siebdruckverfahren auf die Rückseite der Membran aufgebracht werden. Durch den ausgeübten Druck erhöht sich der Widerstand, wenn der Druck das Material verformt. Die Messung der Widerstandsänderung erfolgt über eine Wheatstone-Brückenschaltung.
- bessere Korrosionsbeständigkeit
- deutlich geringere Herstellungskosten im Vergleich zu piezoresistiven Sensoren (kein Öl als Übertragungsmedium notwendig, keine hermetische Abdichtung)
- gute thermische Stabilität (im Vergleich zu piezoresistiven Sensoren)
- Einsatzbereich 2 – 600 bar
Bild: Drucksensor, Metallux SA, www.metallux.ch
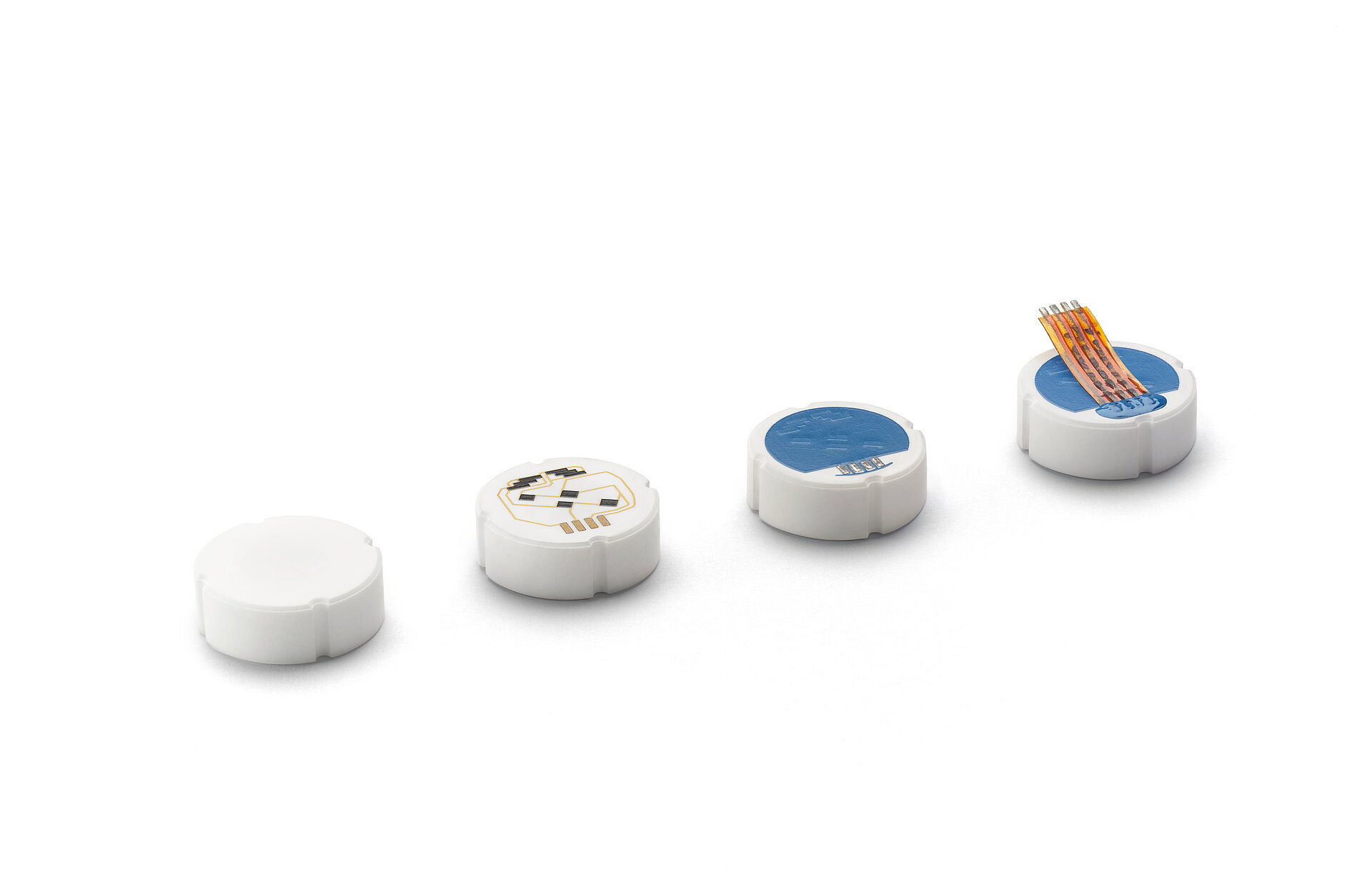